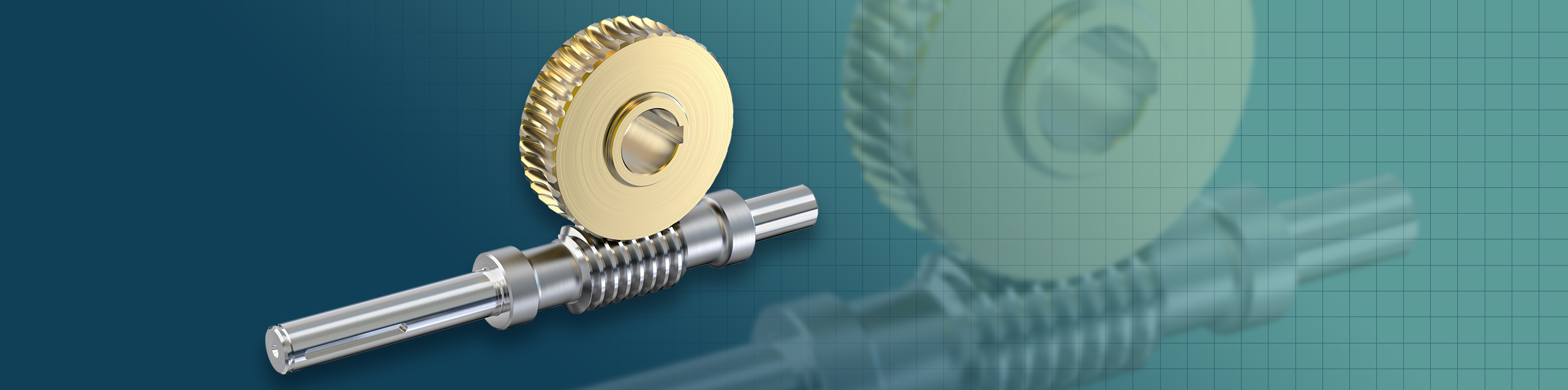
流動解析事例
“強さと精密さの追求”~繊維強化樹脂を使ったギア設計
Summary
- ガラス繊維強化ポリアセタールをウォームホイールへ適用した際の、樹脂CAE解析の活用事例を紹介します。
- 流動反り解析によって、寸法精度の評価方法の1つである真円度を評価し、目標をクリアできることを確認しました。
- 最適形状へ変更することにより、強度を保持しながらも23%の軽量化を可能にしました。
解析の背景
ガラス繊維強化材料は、従来の非強化プラスチックに比べて強度が勝る一方、ガラス繊維が配合されているため比重が大きくなります。また、ガラス繊維強化材料の場合、ガラス繊維の配向を考慮した設計が必要となります。
ここでは、ガラス繊維強化ポリアセタールを樹脂CAE技術を活用し、ウォームホイールへの適用を目指した事例を紹介します。既存品と同等性能を保持しながら、軽量化のための形状変更を実施しました。また、ウォームホイールは寸法精度が非常に重要です。流動反り解析によって、寸法精度の評価方法の1つである真円度を評価し、既存品と同等になることを確認しました。
目的
軽量化のための形状変更
形状変更に伴う真円度の確認
提案内容
図1のように、既存品では強度増加のためにリブがついていました。今回の提案では、リブを排除した設計にしています。これは、既存品の材料よりも弾性率が2.8倍のガラス繊維強化ポリアセタールを用いたためです。剛性の高い材料を用いることで、よりシンプルな形状を提案することができました。
密度は1.09倍と大きくなりますが、リブをなくしたことで23%の軽量化も可能にしています。
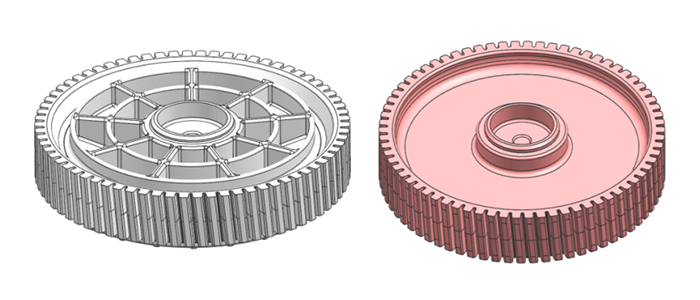
図1 既存形状(左)と提案形状(右)
解析内容
図2の条件で流動解析を実施し、真円度評価を行いました。
既存品には他社材を用いており、提案品にはテナック™-Cガラス繊維強化グレードを用いました。
真円度とは、円形形体の幾何学的に正しい円からの狂いの大きさ(JIS B 0621-1984)のことです。歯車は複数の歯がその3次元形状のかみ合いにより、トルクを伝達する非常にデリケートなメカニズムのため、かみ合う歯車の誤差は伝達特性に悪影響を与えます。各歯先直径を測定し、真円に近くなることが重要です。
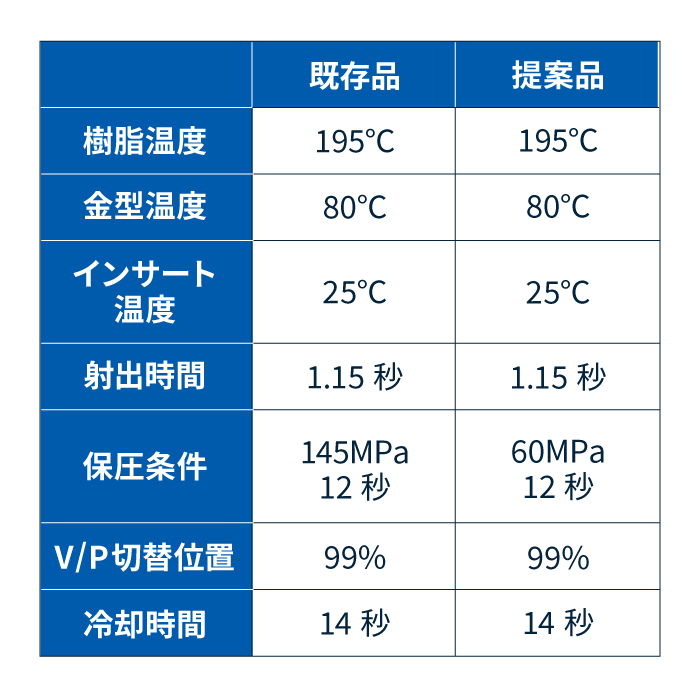
図2 解析条件
結果
図3のように、上中下の3か所で歯先直径を測定し、平均の差異が0.03mmになることを確認しました。差異の条件は0.03mm以下だったため、目標をクリアできました(図4)。
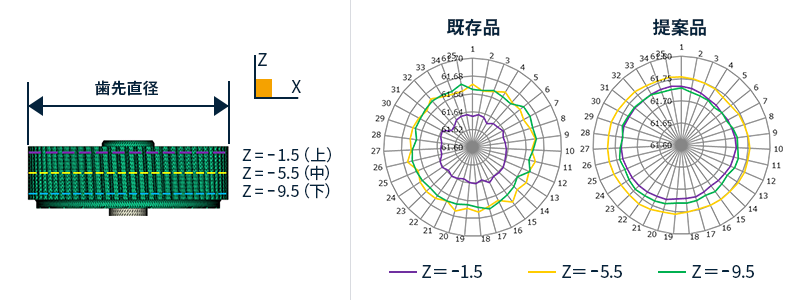
図3 真円度評価位置(左)と真円度評価結果(右)
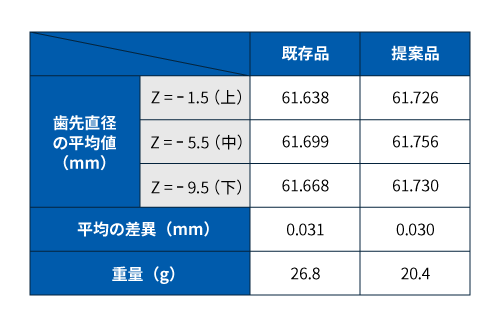
図4 真円度評価結果
ウォームホイールとは
ウォームギヤに用いられるはす歯(斜歯)歯車のことをウォームホイールと言います。ウォームギヤとは、ウォームホイールとウォーム(ネジのような螺旋状の歯がついた円筒状)の2つが直角に噛み合ったものを指します。ウォームホイールは、歯の断面がウォームに食い込むようにRがついている点と、歯筋がウォームに合わせて螺旋状になっているのが特徴です。ウォームギヤのメリットとして、減速比が大きいことや出力トルクが強いことがある一方、摩擦熱や摩耗が発生しやすいというデメリットもあります。
今回提案したガラス繊維強化材料グレードは、従来の強化材と比較して、摩耗が少ないという特徴があったため、提案に至りました。
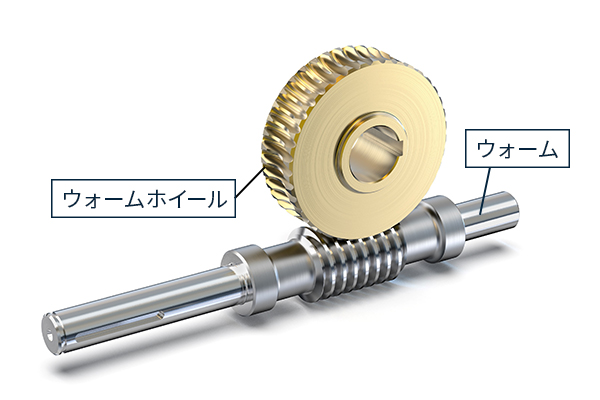
図5 ウォームギヤ
CAE解析に関するご質問、設計変更時のご相談はこちらへ