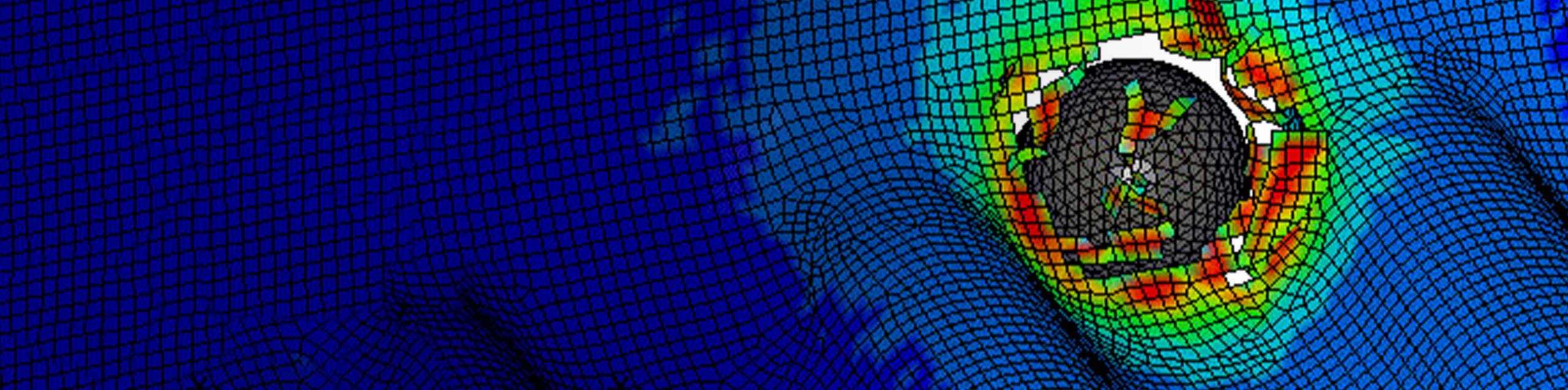
動的構造解析事例
衝撃解析精度検証:オイルパン
Summary
- トポロジー最適化によって当初の金属製に比べ、重量を60%削減した樹脂製オイルパンの性能を評価しました。
- オイルパンは車体下部にありチッピングという現象が生じやすいため、チッピングを想定した実験や解析をすることで、強度の評価をします。
- 跳ね上げられた石を模擬した金属製の弾丸が時速80km/hで樹脂製のオイルパンに衝突する試験を、高速度カメラで撮影しました。同様のシミュレーションを実施し、精度高く再現されることがわかりました。
解析の背景
自動車の軽量化は燃費の向上に直接的につながるため、CO2排出量削減のために非常に重要です。
トポロジー最適化によって当初の金属部品より重量を60%削減したオイルパンの性能を評価しました。
オイルパンは車体下部にあり、前の車がはねあげた小石が当たるなどして破損するチッピングという現象が生じやすいです。
実際にチッピングを想定した実験と解析を比較しました。
Reducing vehicle weight is crucial in reducing CO2 emissions for it directly impacts fuel economy.
We evaluated the performance of a plastic oil pan whose weight was reduced by 60% from the original metal part through topology optimization.
The oil pan, located at the bottom of the vehicle body, is prone to be damaged by stone chipping.
We have compared experimental and analytical results of stone chipping.
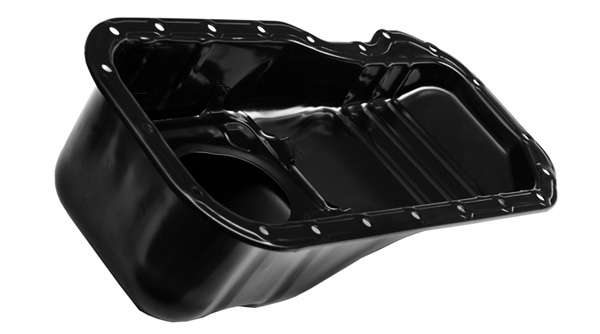
図1 オイルパン
目的
チッピングの実測値と解析値の比較
内容
LS DYNA(Livermore Software Technology社)で衝撃解析を実施しました。
跳ね上げられた石を模擬した金属製の弾丸が時速80km/hで樹脂製のオイルパンに衝突する試験のシミュレーションと、実際の試験を高速度カメラで撮影した様子を比較しました。
衝撃解析では、モデルがどのように固定されているか拘束条件を正しく設けることが重要です。
オイルパンはフランジをぐるっとボルトで固定されるため、解析上ではボルトの穴を完全拘束としました(図2)。
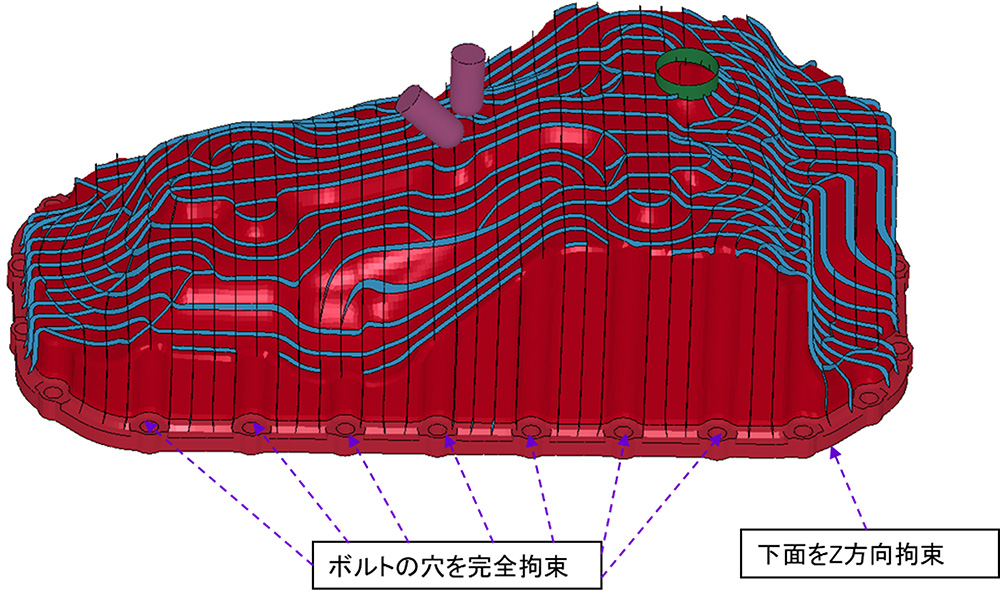
図2 拘束条件
結果
図3の動画を比較すると、解析と実験の様子が合っていることがよくわかります。
試験片ではない実製品に適用しても、高い精度で予測できました。
流動解析の事例でご紹介した精度の高い反り変形後のモデルを用いたことも、高い精度で予測できた一因です。
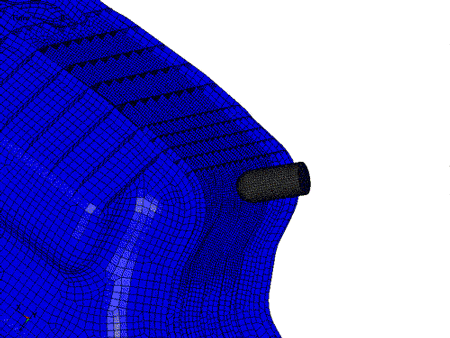
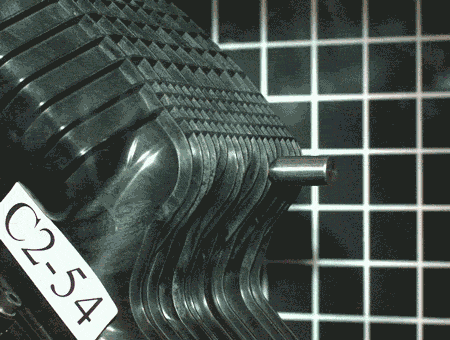
図3 衝撃解析(上)および衝撃試験(下)の比較
補足(材料モデル)
本解析では、材料にレオナTM14G33(PA66、GF33%)を用いています。
レオナTM14G33は熱可塑性樹脂(加熱すると分子鎖が流動して軟化する)の中の結晶性樹脂に分類されます。
結晶性樹脂は、溶融状態から徐冷により球晶を形成し、球晶には分子鎖が折りたたまれた大きさ10nm程度のラメラ状の結晶質部分と、分子鎖がランダムコイル状になった非晶質部分とが混在します。
結晶性樹脂の変形過程では、変形の進展に伴いクレーズという樹脂特有の微視的損傷が観察されます。
こちらの解析を実施した当時は、樹脂材料を対象とした材料モデルが少なく、中には金属材料を対象とした材料モデルを用いてシミュレーションされることもありました。
そこで、弊社では樹脂材料特有のこのクレーズに対応する新たな独自の材料モデルを開発しました(図4)。
材料モデルに用いた構成式にご興味がある方は、こちらの論文をご覧下さい。
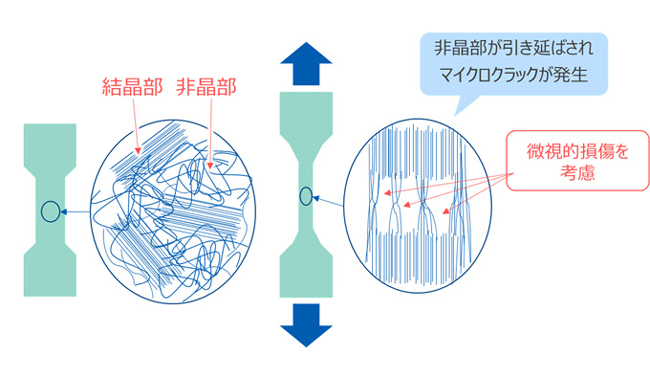
図4 微視損傷モデル
CAE解析に関するご質問・ご相談などはこちらへ
お問い合わせ