- TOP
- CAE解析の基礎知識
- 第6回 樹脂流動解析の解析結果の読み込み方
<連載>プラスチック製品設計のためのCAE解析基礎知識
第6回 樹脂流動解析の解析結果の読み込み方
射出成形シミュレーション(流動解析)の出力結果と、得られた情報を具体的にどのように製品・金型設計や成形工程に生かすことができるのかについて解説します。
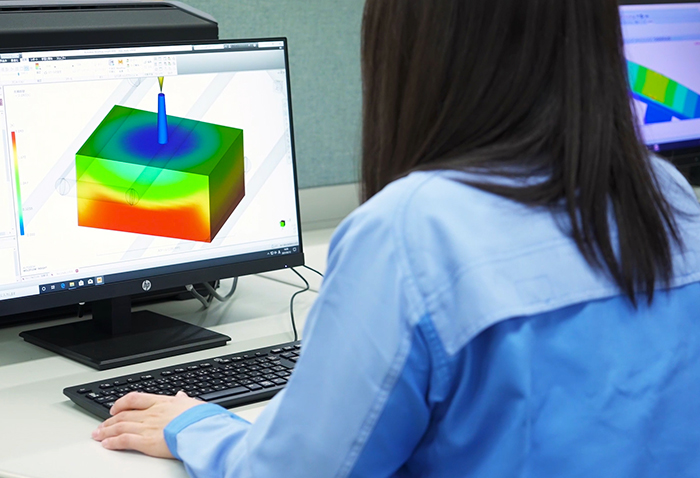
目次
1. はじめに |
2. 射出成形シミュレーションでなにが分かるのか |
3. 解析結果をどのように使うのか |
4. 成形不良や不具合について |
5. まとめ |
はじめに
射出成形シミュレーションは、どのような形でアウトプットされるのでしょうか。シミュレーション結果は一般的にアニメーションやコンター図として表され、視覚的に分かりやすく工夫されています。本記事ではアウトプット情報の種類や、どのように設計やその後の工程に生かすのかということについてご紹介いたします。
射出成形シミュレーションでなにが分かるのか
射出成形シミュレーションは、一般に流動解析と呼びます。流動解析と一口に呼んでも、知りたいことによって実施する解析は異なります。メインの解析は4つあり、冷却解析・充填解析・保圧解析・反り解析と言います。
冷却解析は、射出成形金型内の熱流動を解析するために使用する熱伝達シミュレーションです。樹脂が充填されたキャビティ内の温度や金型全体の温度、冷却時間を定めるのに用いられます。
充填解析は、充填過程の金型内の樹脂の流動を予測します。充填解析では、V/P切替位置に達するまで、射出位置から段階的に伸張していく金型キャビティ内のフロー フロントを計算します。
保圧解析は、保圧過程の金型内の樹脂の流動を予測します。充填解析→保圧解析の順に実行され、キャビティが樹脂で完全に充填されるかを調べることが可能です。
反り解析によって、反りの原因を特定してゲート位置の変更、設計パラメータの変更、肉厚変化の低減などの解決策を検討します。
これらの解析を実施することにより、以下のアウトプット情報を得ることができます。
■ 充填パターン
充填パターンとは、成形品に樹脂がどのように流れるのかを充填解析で可視化した結果です。メッシュモデルにゲート位置、樹脂の種類、解析条件を設定し、樹脂の充填パターンを確認できます。図1のように、モデルにゲートから樹脂が充填されていく様子を、グラデーションによって確認できます。
樹脂が充填されるのに時間がかかる場所が分かるので、適切なゲート位置を検討したり、薄肉部などの流れにくい形状を変更したりするなど、設計に反映できます。
図1 充填パターン例
■ 充填完了時の樹脂圧力分布
キャビティが樹脂で完全に充填されたときのキャビティ内の圧力がどのように分布しているかを充填解析で可視化できます。圧力が不均等にかかると、成形品の変形などの原因となります。また高い圧力が必要な製品では金型の破損につながる恐れがあります。圧力がどの部分にどのようにかかっているかを知ることで、金型設計に生かせます。
図2 充填完了時の樹脂圧力分布例
■ 充填完了時の樹脂温度分布
金型に樹脂を充填完了時、樹脂の温度がどのように分布しているかを、冷却解析・充填解析でシミュレーションした結果です。樹脂温度のばらつきは収縮の不均等の原因となり、成形品の反りなどにつながります。できるだけ均一に冷却されるよう冷却効率や冷却水配管の配置を検討するために用いられます。
図3 充填完了時の樹脂温度分布例
■ フローフロント温度
フローフロントとは金型に注入された樹脂が流れていく際の先端のことを指し、樹脂が成形品の各部到達した時点の温度を示します。冷却解析で計算されます。金型は溶融樹脂より温度設定が低いことが多く、充填過程で樹脂の温度は下がっていきます。充填時のフローフロント温度が低すぎると成形不良の原因となるため、温度変化が少なくなるように調整する必要があります。
図4 フローフロントの樹脂温度例
■ 金型表面温度分布
冷却完了時の成形品表面(金型表面)の温度分布が確認できます。冷却が不均一になっていないか、また金型の固定側と移動側の温度差が大きくないかなどを確認でき反りの原因の考察に使用できます。
図5 金型表面温度分布例
■ 成形品各部の温度の時間変化
成形品各部の温度の時間変化を冷却解析から出力します。変形や反りの原因となるホットスポットやコールドスポットといった温度の偏りがないか、成形品より先にゲートが固化してしまわないかなどを確認します。また、均一に冷却されるかどうかの確認もできます。
図6 成形品各部の温度の時間変化例
■ 成形品各部の圧力の時間変化
成形品各部の圧力の時間変化は充填解析で解析します。通常、充填開始時の圧力は1気圧で、フローフロントが到達した箇所から上昇します。樹脂の種類による流動性の違いや、流動が制限される部分では圧力が上がるため、樹脂の流動が適切であるかを確認できます。また最大圧力を知ることで、成形機サイズの選定に役立ちます。
図7 成形品各部の圧力の時間変化例
■ 反り変形
反り解析では、冷却解析および充填解析の結果を使用して、成形品の収縮および反りがどのように発生するかを予測します。またどの程度の変形が起こるのかをシミュレートします。製品設計段階で、反りの少ない形状やゲート位置などを検討し、設計に反映させることができます。
反り変形は、製品が均一に収縮しないことで発生します。主な要因は3つあり、冷却差・収縮差・配向差です。Moldlfowでは反りの原因の特定オプションをオンにすることで、主要因に関する情報が出力されるようになります。図8は全要因の情報を出力した結果です。
図8 反り変形例
■ V/P切替時の圧力
V/P切替とは、スクリューで溶融樹脂を金型に注入する際に、射出工程(速度制御:Velocity control)から保圧工程(圧力制御:Pressure control)へ切り替わることを言います。
V/P切替時の圧力結果から、速度制御の充填過程でどこまで樹脂が充填されるかがわかります。速度制御過程では、キャビティ内に樹脂は完全に充填されていない状態であることが望ましく、未充填箇所には、圧力制御で射出圧力をコントロールしながら補充します。このときの保圧力が低いとヒケの原因となり、高すぎるとバリや金型破損を引き起こす恐れがあります。
充填解析で解析することで、適切な成形条件を求めることができます。
図9 V/P切替時の圧力例
■ 射出位置の圧力
充填と保圧工程における、成形品各部の圧力の時間変化を解析します。成形品内の特定箇所、もしくは多数個取りでは一部の成形品に圧力の不均等があった場合、流動のアンバランスがある可能性があります。流動に問題がないか、また保圧が適切であるかを確認します。
図10 射出位置の圧力例
■ 型締め力
型締め力とは、樹脂を充填する際に金型を締めておくのに必要な力の大きさのことです。成形品全体の圧力分布から適切な値を求めます。成形する際に必要な型締め力から、適切な大きさの成形機を選定するために必要となります。
図11 型締め力例
■ 繊維配向テンソル
ガラス繊維を配合した樹脂では、繊維の配向によって収縮の不均等や、強度の弱い方向ができるなどの問題が起こります。繊維強化樹脂の場合、繊維配向解析を用いることで、成形プロセス終了後の繊維の方向や配向テンソル(配向度)を求めることができます。繊維強化樹脂の特性を生かすためには、配向の傾向を事前に把握しておくことが大切です。
図12 繊維配向テンソル例
■ ヒケ予測
充填解析と保圧解析から、成形品のヒケの出やすい場所やその深さを予測します。ヒケは通常、成形品厚肉部やリブ、ボス、内部フィレットなどの反対側に発生します。形状やゲート位置、金型や樹脂温度を下げるなど成形条件を変えて解析することで、ヒケの原因を特定し対策を取れます。
図13 ヒケ予測例
■ ウェルドライン予測
充填解析でウェルドラインの発生箇所を予測します。ウェルドラインは樹脂が合流した部分に現れます。強度不足や外観不良となることから、ゲート位置の調節によって外側から見えにくい場所に移動させたり、会合角(樹脂がぶつかる角度)を緩やかにしたりすることで目立ちにくくできます。
図14 ウェルドライン予測例
解析結果をどのように使うのか
流動解析で得られたこれらの情報は、具体的にどのように製品・金型設計や成形工程に生かすことができるか解説します。判断が必要となる場面において、解析データを用いることで客観的に合理的な指標を得られます。
■ 必要な成形機のサイズ
適切な成形機のサイズを知るためには、型締め力、射出圧力などの適切な大きさを知ることが重要です。流動解析を用いることで、それらの値を知り、成形機のサイズを事前に検討できます。成形機のサイズは成形スケジュールやコストに直結するため、生産計画を立てる上で必要です。
■ 成形可否判断
充填パターン、圧力、樹脂温度などから、成形品に樹脂が過不足なく充填できるのかどうかを確認します。流れにくい薄肉部やランナーを調整したり、樹脂の種類を変えるなどしたりして事前に検討し、対策を行うことで、成形段階でのトラブルを減らすことに貢献します。
■ ゲート位置の最適化
充填パターンやウェルドラインなどから、どの位置にゲートがあれば成形しやすく、不良が起きないのかを検討します。ゲート位置の変更によって、ほかのトラブルが起きないかどうかということも確認し、優先順位を付けて判断し最適な位置を決めることが大切です。
■ 成形条件の最適化
V/P切替時の圧力、射出位置、金型温度、冷却速度から最適な成形条件を導き出します。成形条件の設定には、経験や知識を必要とするため成形技術者のスキル頼みになってしまうことがありますが、あらかじめ適切な成形条件を算出することで、成形工程における効率化につながります。
■ 金型冷却の最適化
金型温度分布や温度の時間変化から、できるだけ均一に金型が冷却されるよう、水管位置の調整、冷却水の温度調整をします。冷却不足や冷却の不均等は成形不良の原因となる恐れがあり、適切な冷却は重要です。生産開始後に成形トラブルが発生した場合、水管の変更など金型の大がかりな変更をすることは難しいため、事前に十分に検討して対策することが大切です。
■ 上記最適化による反り変形量の改善
圧力の不均等や冷却の不均一、繊維の配向などによって、成形品に反りが発生してしまうことがあります。特に厳密な寸法精度が必要とされる製品では、流動解析によって事前にできる限り検討し、対策しておくことで変形量を抑えることが可能です。
成形不良や不具合について
流動解析を用いることで、起こりうる成形不良や不具合を予測できます。量産成形をする上で、成形不良は避けては通れない問題ですが、その発生を最小化することに役立ちます。ここではよくある成形不良をご紹介します。
■ ショートショット
ショートショットとは、溶融した樹脂が金型の先端まで完全に充填されないという成形不良を指します。ショートショットが発生した成形品のリカバリーはできません。ショートショットの原因は、樹脂の流動が足りない、射出圧力や保圧が不足していることなどです。V/P切替位置の調節、射出圧力、ゲート位置の調節によって発生を抑制します。
図15 ショートショット例
■ ウェルドライン
成形品内に充填された溶融樹脂の合流部分が、薄い傷のような線状になることがあり、それをウェルドラインと言います。ウェルドラインの箇所は強度が弱く、強度試験などの際に破損してしまう恐れがあります。また外観上でも傷のように見えてしまうことから、消費者クレームにつながる恐れがあります。ゲート位置を変更し、目立つ箇所に出ないようにしたり、金型温度の調節や、成形品の肉厚を調整したりして会合角をコントロールすることによって対策します。
図16 ウェルドライン例
■ ガス焼け
ガス焼けとは、成形品の一部が焼けて黒く炭化してしまう現象のことです。溶融樹脂が高圧で注入されることで、キャビティ内の空気が行き場を失って圧縮され、高熱を発することで発生します。ガス焼けは成形初期ではなく、量産が軌道に乗ったころに発生しがちで、成形工程ではガス焼け対策に頭を悩ませていることも少なくありません。射出速度を落とすだけでなく、ガスを抜くためのエアベントを設ける、ゲート位置や肉厚で樹脂の流動をコントロールする、といった対策が有効です。
図17 ガス焼け例
■ ヒケ
ヒケとは外観不良の一つで、成形品の肉厚が異なる箇所などに収縮率の差が生じることで発生します。ゲート位置の調整、射出圧力や保圧を上げる、冷却効率、肉厚の調整によって対応します。リブやボスなど肉厚部に発生しやすいため、設計段階で対策をしておくことが重要です。
図18 ヒケ例
まとめ
製品設計や金型設計段階で、成形工程で起こりうる問題をシミュレーションして対策を取っておくことが大切です。そのためには設計者も成形についての知識が必要になります。成形性を考慮した設計を行うことで、手戻りを減らし、開発期間の短縮に直結します。成形トラブルは、成形工程だけで全て解消できるわけではありません。設計段階から対策を行うことが必要です。CAEのシミュレーション結果の使い方を知り、ぜひ設計に生かしましょう。
次回は「成形不良の予測」についてご説明します。
CAEに関するお問いわせはこちらから