- TOP
- Fundamentals of Sustainability in Plastics
- Part 1 - What is the mass balance method?
Fundamentals of Sustainability
Part 1 - What is the mass-balance method?
We will introduce the concept of the mass balance method, familiar examples, and benefits.
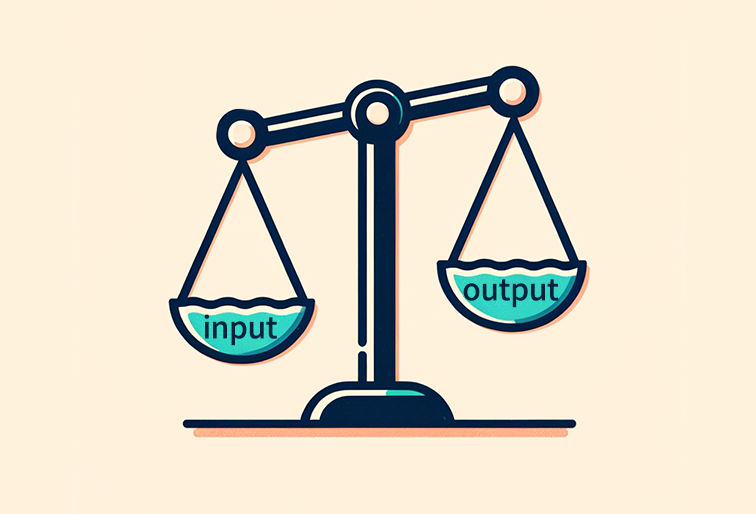
What is the mass-balance method?
The mass-balance method (also known as the mass-balance approach) is a chain of custody that allows tracking the total amount of raw materials with certain properties (such as materials derived from biomass or from recycled plastics) as they move through a production system or supply chain and ensures an appropriate allocation of these raw materials to the finished goods.
*出典:バイオプラスチック導入ロードマップ -持続可能なプラスチックの利用に向けて-(環境省、経済産業省、農林水産省、文部科学省)(令和3年1月)
The mass-balance method is a framework for ensuring accuracy by carefully controlling the balance of raw materials received as inputs and final products produced as outputs. For example, suppose we blend 4 tons of biomass-derived raw materials with 8 tons of petroleum-derived raw materials to produce 12 tons of a final product. Based strictly on the blend ratio, we have produced 12 tons of a product that is 33% (or one-third) biomass-derived. However, in the mass-balance approach, we can allocate 4 of those 12 tons to be designated 100% biomass-derived product, while the remaining 8 tons are designated petroleum-derived plastic.
Mass balance method diagram
The segregation approach
The term segregation refers to the conventional production approach in which raw materials received as inputs are used as-is, without modification, in the products produced as outputs. This is the way things were traditionally done. In the example discussed above, the 12 tons of product produced from 33% (or one-third) biomass-derived ingredients would be sold in just that way—as 12 tons of 33% biomass-derived product.
There also exist several other approaches; for more details, see What is the Chain of Custody? (link)
Thus, even for production processes in which biomass-derived raw materials are blended with petroleum-derived raw materials, adopting the mass-balance approach allows some portion of the final product—proportional to the fraction of biomass-derived materials in the input blend—to be designated fully biomass-derived.
Note that ISO 22095:2020(en) Chain of custody — General terminology and models refers to the mass-balance method as the mass-balance model; it is one of several existing models for managing supply chains throughout what is known as the chain of custody, including processing and logistics at all stages from raw materials to final products.
Mass-balance methods in everyday life
The mass-balance method has already begun to make inroads in many industrial sectors, including several that play familiar roles in everyday life: FSC certification in the paper and pulp industry, RSPO certification for palm oil, and fair-trade certification for cocoa beans and similar products are just a few examples of the increasingly ubiquitous adoption of mass-balance techniques.
In the case of palm oil, for example, carefully balancing the volume of certified palm-oil inputs against the volume of final-product outputs allows supplies of certified palm-oil to be controlled throughout the entire marketplace, even if non-certified palm oil is blended with certified palm oil from RSPO-certified plantations during the logistical process.
As customers preferentially select RSPO-certified palm-oil products, demand for RSPO-certified palm oil will grow across the market, resulting in more and more RSPO-certified plantations—and driving the entire supply chain toward a sustainable model.
Advantages of the mass-balance method
Biomass plastics suffered from several disadvantages: they required specialized production equipment and specialized raw materials, they applied to only a restricted range of products, and their diffusion throughout the marketplace was rather slow. The adoption of mass-balance methods for plastic products allows producers the option of gradually replacing existing materials with more sustainable resources, a promising development on the road toward future carbon-neutral societies. Key advantages of mass-balance production for plastics include the following:
- Reduced environmental footprint : Promoting the use of biomass-derived materials decreases consumption of fossil-fuel resources. Moreover, atmospheric CO2 remains fixed during the biomass growth process, and—as long as biomass is re-manufactured—burning biomass does not increase atmospheric CO2, thus helping cut CO2 emissions overall.* Plus, this scheme is not limited to biomass-derived ingredients: it can also be used to incorporate resources derived from waste products.
- Uses conventional processes at existing facilities: Other than blending biomass-derived substances into input materials, no modifications to production processes are necessary; existing facilities and processes can be used in the same ways and under the same conditions as before. This ensures that physical properties and other characteristics of products are equivalent to those of their conventional counterparts. In contrast, production by segregation approach requires complete separation between biomass-derived ingredients and petroleum-derived ingredients; this adds cumbersome additional process steps such as subdividing production vats and temporarily halting production to clean vats when switching between biomass and petroleum materials.
- Applicable to a wide range of products: The mass-balance approach allows biomass to be introduced into many different types of production processes—including processes involving materials that were traditionally difficult to source from biomass (such as derivative substances requiring multiple distinct processes to produce), of which naphtha is perhaps the most basic example.
Challenges of mass-balance methods
Despite the many advantages noted above, the adoption of mass-balance methods does pose some challenges, including the following:
- Traceability and reliability : A robust reliability framework—spanning the entire supply chain to verify that biomass-derivative materials are properly incorporated into production processes, that manufactured products are properly allocated for various designations, and that other key provisions are upheld—is an essential prerequisite for mass-balance operations. The gold standard for ensuring reliability is to pursue auditing and certification by external international certification bodies such as ISCC, RED cert, and RSB.
- Awareness: Because the mass-balance philosophy is relatively new, producers must pursue outreach efforts to educate consumers and corporate partners. In the past, biomass certification protocols determined biomass content based on the proportion of biomass-derived ingredients actually contained in products, and products were labeled with biomass-content statistics determined in this way. This is appropriate for conventional segregation-based production, in which the displayed biomass content of a product does in fact coincide with the proportion of biomass it contains. In the mass-balance approach, by contrast, biomass content is determined by allocation and designation, as discussed above, and this will be a new and unfamiliar concept for many consumers. Going forward, it will be important to change how biomass content is expressed and displayed—and how products are positioned and described.
- Economics: Although the mass-balance approach makes it much easier for manufacturers to incorporate biomass-derived ingredients into their production processes, the unfortunate reality is that many biomass-derived materials remain considerably more expensive than petroleum-based alternatives. As biomass-derived products continue their gradual penetration into existing markets, we expect to see increased production of biomass-derived raw materials, helping producers deliver goods at more accessible prices.
Resin materials using biomass-derived ingredients via mass-balance approach (ISCC PLUS certified)
Asahi Kasei is developing engineering plastics that use biomass-derived ingredients via mass-balance approach. These materials have earned certification under ISCC PLUS*, an international certification program for sustainable products.
XYRON™ PPE using biomass-derived raw material
Our XYRON™ modified PPE resins have earned ISCC PLUS certification as PPE materials whose ingredients include methanol/phenol derived from biomass via mass-balance approach.
Because biomass-certified PPE resin retains properties on par with those of conventional petroleum-based PPE resin (including heat resistance, flame retardance, low weight, electrical insulation, dimensional stability, and low water absorption), they can help to achieve sustainability in a wide range of application domains.
TENAC™ POM resin by using biomass raw material
By acquiring ISCC PLUS certification, we can produce and sell POM resin using sustainable raw material assigned by the mass-balance method.
By applying the mass balance method, we are able to support our customers around the world in their efforts for sustainability while maintaining the excellent performance of POM resin (friction and wear properties, strength and rigidity, resistance to oil and organic solvents, etc.).
*ISCC (International Sustainability and Carbon Certification) is an international certification system that offers solutions for the implementation and certification of waste and residue raw materials, non-bio renewables and recycled carbon materials and fuels. ISCC PLUS is a certification system that covers mainly bio-based carbon materials which are produced outside of the EU and supplied globally, and to manage and ensure sustainable raw materials in the supply chain.
If you are interested, please feel free to contact us.