- TOP
- Sustainability
- Producing materials
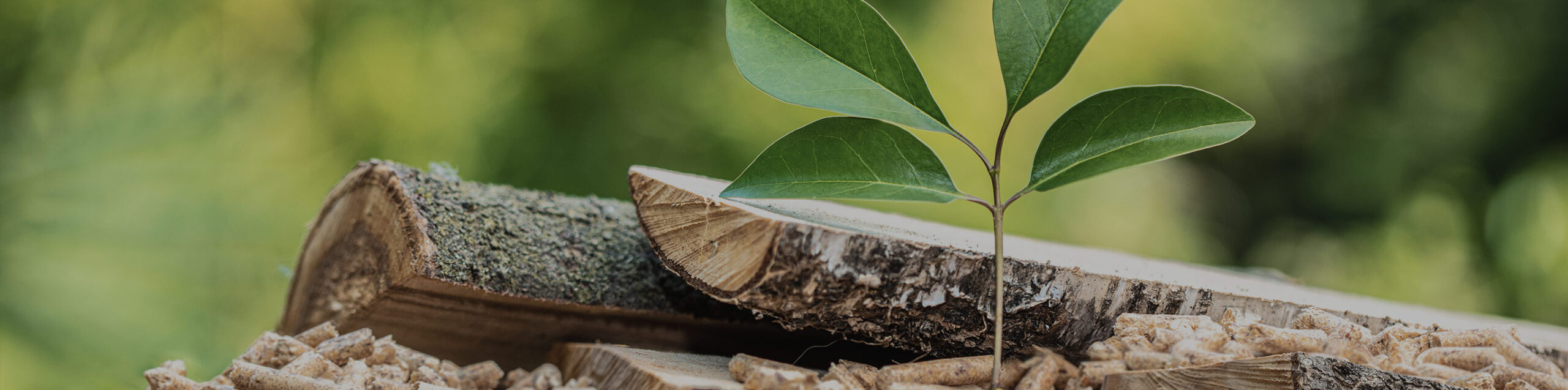
Sustainability
Producing materials
Summary
- A key step toward establishing plastics as renewable resources will be to increase the share of plastics derived from biomass and recycled materials instead of conventional petroleum-derived plastics
- Biomass plastics are plastics made from biomass (plants and other reusable organic resources) ingredients. In recent years, environmental considerations have created extremely high societal demand for these materials.
- Cellulose nanofibers (CNFs) are fibers with a width of 3-100 nm and a length of less than 100 μm, and are obtained by separating fibers of cellulose, the primary constituent of plants. CNFs have several excellent properties, including low weight and high strength; moreover, as renewable resources they are biodegradable and recyclable and offer other similar advantages.
- Asahi Kasei is developing a variety of engineering plastics using biomass-derived ingredients, with special efforts devoted to achieving compliance with the ISCC PLUS international certification. We are also working to develop light-weight materials by combining highly heat-resistant cellulose nanofibers with various types of engineering plastics.
Steps toward establishing plastics as renewable resources
A key step toward establishing plastics as renewable resources will be to increase the share of plastics derived from biomass (plants and other reusable organic resources) and recycled materials* instead of conventional petroleum-derived plastics.
On this page we introduce two classes of sustainable materials that have emerged in recent years as particularly attractive candidates: biomass plastics and CNFs.
*Plastics derived from recycled materials are discussed in more detail on page 5. Recycling materials.
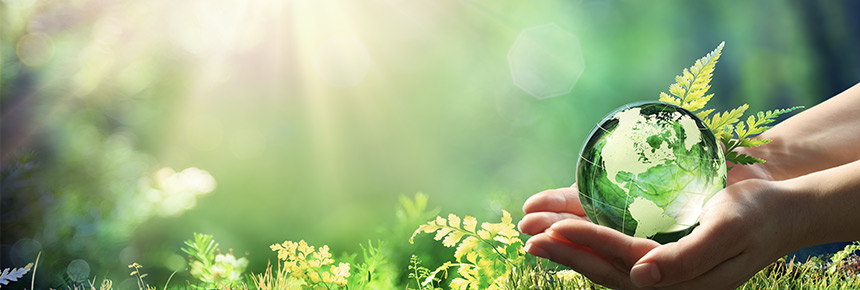
Biomass plastics
■ What are biomass plastics?
Biomass plastics are made from biomass (plants and other renewable organic resources) ingredients.
■ Growing social demand of biomass plastics
A key step toward establishing circular economy will be rapidly increasing the share of all plastics derived from biomass (plants and other renewable resources) and recycled materials instead of conventional petroleum-derived plastics.
One of the Plastics Material Cycle Strategy proposed by the Japanese government in May 2019 is to replace the raw materials currently used to produce plastic packages, plastic wrappers, and other plastic products with materials such as biomass plastics that are made from renewable resources. To encourage and accelerate this transition, Japan has also set a specific numerical goal: to use as much biomass plastic as possible— 2 million tons—by 2030.
*Source: Japanese Ministry of the Environment, Roadmap for bioplastics introduction: For the sustainable use of plastics
Cellulose nanofibers (CNFs)
■ What are cellulose nanofibers (CNFs)?
Cellulose nanofibers (CNFs), also known as microfibrillated cellulose or cellulose nanofibrils, are fibers with a width of 3-100 nm and a length of less than 100 μm obtained by separating fibers of cellulose, the primary constituent of plants. Plant-derived CNFs are typically produced from wood, but may also be obtained from grass, seaweed, bamboo, or other raw ingredients.
■ Key features of Cellulose Nanofiber (CNFs)
CNFs have several excellent properties, including light weight and high strength; moreover, their production from cellulose ensures that CNFs are renewable resources that are biodegradable and offer other advantages.
CNFs have attracted significant attention as an additive for compound resins—an application in which the highly recyclable nature of CNFs stands out as a major advantage over the glass fibers conventionally used to enhance the strength of resin products.
Asahi Kasei’s Recommended Solutions (1)
Engineering plastics using biomass-derived ingredients
To cut greenhouse-gas emissions and reduce usage of petroleum resources, Asahi Kasei is actively developing engineering plastics using biomass-derived ingredients.
Resin materials using biomass-derived ingredients via mass-balance approach (ISCC PLUS certified)
Asahi Kasei is developing grades of our XYRON™ modified PPE and TENAC™ POM resins that use biomass-derived ingredients via mass-balance approach (*1). These materials have earned certification under ISCC PLUS (*2), an international certification program for sustainable products.
PPE using biomass-derived raw material
Our XYRON™ modified PPE resins have earned ISCC PLUS certification as PPE materials whose ingredients include methanol/phenol derived from biomass via mass-balance approach.
Because biomass-certified PPE resin retains properties on par with those of conventional petroleum-based PPE resin (including heat resistance, flame retardance, low weight, electrical insulation, dimensional stability, and low water absorption), they can help to achieve sustainability in a wide range of application domains.
We are also developing recycled XYRON™ grades combining PPE with recycled resins, working with customers to design recycling schemes, and pursuing a variety of other initiatives to assist in building sustainable future societies.
TENAC™ POM resin by using biomass raw material
By acquiring ISCC PLUS certification, we can produce and sell POM resin using sustainable raw material assigned by the mass-balance method.
By applying the mass balance method, we are able to support our customers around the world in their efforts for sustainability while maintaining the excellent performance of POM resin (friction and wear properties, strength and rigidity, resistance to oil and organic solvents, etc.).
(*1)ISCC (International Sustainability and Carbon Certification) is an international certification system that offers solutions for the implementation and certification of waste and residue raw materials, non-bio renewables and recycled carbon materials and fuels. ISCC PLUS is a certification system that covers mainly bio-based carbon materials which are produced outside of the EU and supplied globally, and to manage and ensure sustainable raw materials in the supply chain.
(*2) In the case of a mixture of sustainable raw materials and fossil fuel-derived raw materials in the production process, the portion of sustainable raw material is assigned to certain products based on ISCC PLUS System Documents and its recognized management methods.
Plant-derived polyamide (PA) 610 LEONA™ BG-Series
Polyamide (PA) 610 is a biomass plastic featuring a 60% plant-derived polymer content. The primary grades of Asahi Kasei’s LEONA™ family of PA products are based on PA66, which is made from two raw ingredients: hexamethylenediamine and adipic acid. PA610 is also made from two raw ingredients: hexamethylenediamine and sebacic acid. Sebacic acid is derived from castor oil, a type of vegetable oil obtained from the ricinus plant. Thus, PA610 is a biomass polyamide whose polymer content is 60% plant-derived. Compared to PA66, PA610 contains a longer chain of molecule and has two key properties:
1. Lower water absorption and better dimensional stability.
2. Higher chemical resistance and calcium-chloride resistance
These properties make PA610 well suited for applications to a variety of components, including automobile radiator tanks, various types of pumps, sensors, and battery components.
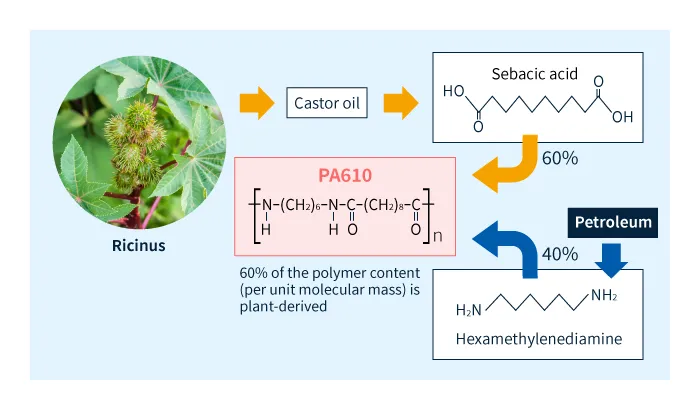
- LEONA™ BG230 (PA610+GF33%) See technical datasheet
Trials for commercialization of polyamide 66 made using biomass-derived intermediate
Asahi Kasei currently uses fossil fuel–derived HMD as an intermediate to manufacture LEONA™ polyamide 66 (also called nylon 66), an engineering plastic featuring outstanding heat resistance and rigidity.
As the world moves toward carbon neutrality, attention is increasingly focused on solutions for reducing greenhouse gas emissions from chemical products derived from fossil fuels. The strategic alliance with Genomatica provides Asahi Kasei with preferential rights to access the early volume of bio-HMD to evaluate the possibility as a feedstock of polyamide 66, enabling Asahi Kasei to accelerate trials of polyamide 66 made using biomass-derived intermediate. Genomatica has an established track record of commercializing manufacturing technology for various chemical products using biotechnology. By using this bio-HMD with its own polyamide 66 polymerization technology, Asahi Kasei aims to support its goal to be first-to-market with more sustainable polyamide 66 made using biomass-derived intermediate for the automotive and electronics application of plastics components and industrial fiber.
- Download related press releases from this link.
Asahi Kasei's Recommended Solutions (2)
CNF-reinforced thermoplastic resins
CNF-reinforced thermoplastics are composite products that combine Asahi Kasei’s highly heat-resistant cellulose nanofibers (CNFs) with various types of engineering plastics—such as polyamide (PA) and polyacetal (POM)—to yield lightweight materials boasting excellent regrindability .
Key features of Asahi Kasei’s CNFs
The CNFs developed by Asahi Kasei are biomass fibers containing cotton-linter constituents that are miniaturized via sophisticated techniques to sizes as small as nanometer scales.
As indicated by the figure on the right, Asahi Kasei’s CNFs can reinforce resins by serving as biomass fillers with higher heat resistance than conventional CNFs. These materials have good recycling properties—they can be recycled for use as ingredients in the same products—and boast low specific gravity (1.5 g/cm3). Other superior properties of these materials include high elasticity, a low linear expansion coefficient, a low friction coefficient, low abrasion, and high gas-barrier strength.
Asahi Kasei’s technologies for nanodispersing CNFs
Because CNFs are extremely hydrophilic, they tend to clump together when blended into resins. This has often prevented CNFs from achieving their full potential as reinforcing additives.
Asahi Kasei is developing technologies for nanodispersing CNFs in a variety of resins, ensuring a single, consistent manufacturing process from CNF production to CNF composites.
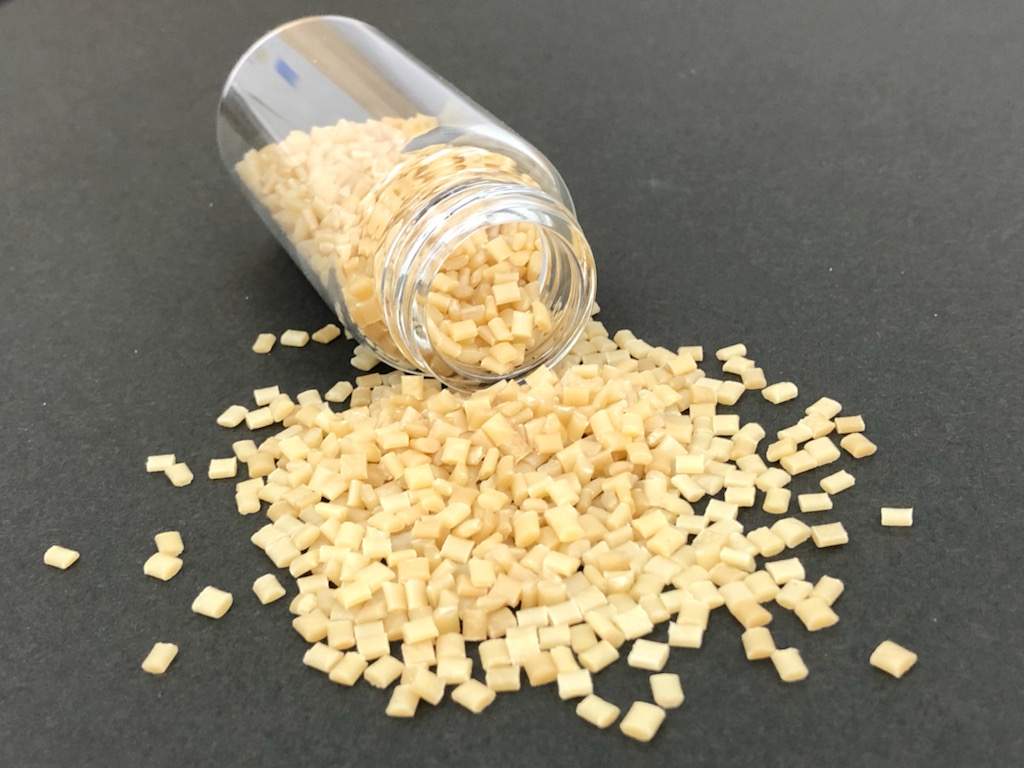
- Go here for details on CNF-reinforced thermoplastics
Please feel free to contact us with your questions.
Inquiries