- TOP
- CAE解析の基礎知識
- 第3回 CAE解析ソフトウェアの紹介
<連載>プラスチック製品設計のためのCAE解析基礎知識
第3回 CAE解析ソフトウェアの紹介
解析対象分野ごとに、その目的と用途について解説すると共に、代表的なソフトウェアと旭化成で使用しているソフトウェアを紹介します
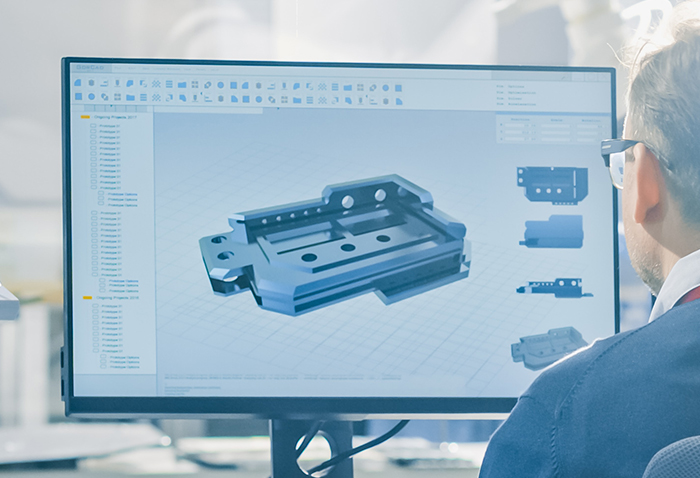
目次
1. 流動解析(流動反り解析) | 9. クリープ解析 |
2. 応力解析 | 10. 応力緩和解析 |
3. 熱伝導解析 | 11. 衝撃解析 |
4. 熱応力解析 | 12. トポロジー最適化 |
5. 熱流体解析 | 13. 音響解析 |
6. 固有値解析(固有振動数解析) | 14. 機構解析 |
7. (周波数)応答解析 | 15. 繊維配向マッピング |
8. 繰り返し疲労解析 |
はじめに
CAE解析向けに国内外の多くのソフトウェア会社から多種多様なソフトウェアが発売されています。どのような解析ができるのか、得意分野、サポート体制など、ソフトウェアによって違いがあり、目的や用途に合った適切な解析ソフトウェアを選ぶことが大切です。
今回は、プラスチックのCAE解析に使われるソフトウェアについて解説します。解析対象分野ごとに代表的な解析ソフトウェア、さらには旭化成で使用しているソフトウェアについてもご紹介します。
流動解析(流動反り解析)
流動の可否、最適ゲート位置の検討や、反りの予測、成形サイクル予測、型締め力予測、冷却効率の良い冷却管を設計するためのシミュレーションです。樹脂流動解析とも言い、製品設計や金型仕様設計においてプラスチック製品の解析では一般的な解析です。
反り変形は重大な成形不良の一つです。反りはキャビティ内で不均一に樹脂の収縮が起こるために発生します。つまり、キャビティ内で温度や圧力が均一になるように成形品の形状やゲート位置を設計し、金型内の温度差がないように金型の冷却管を配置しなければなりません。
図1 流動反り解析例(反り予測)
代表的なソフトウェアにはAutodeskの「Moldflow」、CoreTech Systemが開発した「Moldex3D」、東レが開発した「3D TIMON」などがあります。
旭化成では普及率が高い「Moldflow」を使用しています。
応力解析
荷重をかけたときの変形量や応力、歪み、破壊の有無、破壊荷重を予測するために使用します。機械設計においては製品の強度を知るために必要で、重要度が高い解析です。実際にサンプルを作成して強度試験を行う前にシミュレートすることができるため、設計開発期間の短縮につながります。
図2 応力解析例
応力解析については、別章でさらに詳しく解説します。
代表的なソフトウェアはDassault Systèmesの「Abaqus」、Siemens Softwareの「NX Nastran」、Ansysの「ANSYS」、Altair の「OptiStruct」がありますが、多種多様のソフトウェアが存在します。
旭化成では「Abaqus」とHexagonの「Marc」を使用しています。
熱伝導解析
個体内部の熱の伝わり方を解析し温度分布をシミュレーションします。熱が加わる部位や、発熱する部品などと接する部品で、熱がどのように伝わるのかを解析します。樹脂材料の断熱性や保温性を評価できます。
図3 熱伝導解析例
熱応力解析
温度変化により発生する応力を予測します。
第2回 プラスチックCAEのポイント「2.プラスチックと金属の違い ■温度特性」で述べたように、プラスチックは線膨張係数が金属に比べて大きく、熱応力の影響も大きくなります。線膨張係数が異なる素材と組み合わせた際には、特に注意が必要です。
熱伝導解析で温度分布を求めて応力解析の境界条件として利用する、連成解析を行うこともできます。
熱伝導解析・熱応力解析は、上述の応力解析のほとんどのソフトで計算ができます。
熱流体解析
液体や気体などの流体が対象物の内外をどのように流れるかを予測します。実際に熱が発生する製品の場合、熱が固体の内部を伝わるだけではなく、熱を持った流体(空気、油など)を通して他の部品へ熱が伝わる現象が起こります。そういった現象は熱伝導解析では解析できず、熱流体解析を用います。
また、部品が複雑な形状の場合も、周囲の空気の対流が起こることにより熱伝導係数や温度分布が変化するため、熱流体解析を行うことが有効です。
図4 熱流体解析例
代表的なソフトウェアはAltairの「AcuSolve」、Ansysの「ANSYS Fluent」、Siemens Softwareの「STAR-CCM+」、Convergent Scienceの「Converge」などがあります。
旭化成では「AcuSolve」を使用しています。
固有値解析(固有振動数解析)
物体の固有振動数と固有モード形状を算出します。
固有振動数とは、物体(振動系)が自由振動する際に、1秒間に振動する回数のことです。固有モード形状とは固有振動数で振動しているとき、どのようなかたち(変形)で振動するかというものです。
物体に共振が発生した場合には破損や騒音などの影響を及ぼす恐れがあります。共振とは、物体の固有振動数と同じ振動を外部から受けることで、振動が大きく増幅される現象です。固有振動数解析によって共振が発生しそうな周波数を求めることができ、共振を起こさないような構造設計をするために使用します。
図5 固有値解析(固有振動数解析) 例
(周波数)応答解析
物体が加振されたときの変位や、発生する応力をシミュレーションします。
共振が発生した際、振れ幅や応力がどの程度発生するかを求めることができ、また共振対策をした場合の効果を確認できます。
図6 (周波数)応答解析例
固有値解析(固有振動数解析) ・(周波数)応答解析の代表的なソフトウェアはDassault Systèmesの「Abaqus」、Siemens Softwareの「NX Nastran」や、Ansys の「LS-DYNA」などがあります。
旭化成では「Abaqus」、Hexagonの「Marc」を使用しています。
繰り返し疲労解析
繰り返し荷重をかけた際に、破壊されるまでの回数を予測します。
物体に繰り返し荷重を加えると、静的強度よりも小さい応力でも破壊されてしまうことがあります。これを疲労破壊といい、S-N曲線で評価することができます。
実際にサンプルを作成して耐久性試験を行う前にシミュレートすることができ、開発期間の短縮につながります。
クリープ解析
一定時間後のクリープ変形量を予測します。
第2回 プラスチックCAEのポイント「2.プラスチックと金属の違い ■粘弾性特性<クリープ>」で述べたようにプラスチックは粘性の特性からクリープ荷重の影響が強いため、事前にシミュレーションすることで対策することができます。はんだ接合部の寿命予測などにも使用されます。
応力緩和解析
一定時間後の応力値を予測します。第2回 プラスチックCAEのポイント「2.プラスチックと金属の違い ■粘弾性特性<応力緩和>」で説明した通り、応力緩和はプラスチックの粘弾性特性によって起こる現象です。
ネジやボルトで固定している部位や、バネなど意図的に変形を与えて発生した反力を利用する製品では、設計の際に注意が必要です。クリープと異なり、外部から見ても変化が分からないため、事前に解析を行うことで品質トラブルを防ぐことができます。
繰り返し疲労解析・クリープ解析・応力緩和解析の代表的なソフトウェアはDassault Systèmesの「Abaqus」、Siemens Softwareの「NX Nastran」やAnsysの「LS-DYNA」です。
旭化成では「Abaqus」、Hexagonの「Marc」を使用しています。
衝撃解析
物体が衝突したときや、落下したときの時刻歴発生応力や歪み、変位、加速度などをシミュレーションします。物体は衝撃を受けると、静的応力値の何倍もの大きな応力が発生し、破損などの原因となります。
また材料固有の動的特性(歪み速度依存性、粘弾性効果)を考慮した評価をすることができます。歪み速度依存性とは、変形速度によって材料物性が大きく異なるという樹脂が持つ特性のことです。
自動車などの衝突速度を想定した試験などに使用されます。
図7 衝撃解析例
代表的なソフトはAnsysの「LS-DYNA」、ESIの「PAM-CRASH」、Altairの「Radioss」です。
旭化成では「LS-DYNA」を使用しています。
トポロジー最適化
トポロジー最適化とは、製品の利用シーンで想定される構造的な制約、荷重、拘束条件を与えることで、最適な形状を計算するシステムです。
人では考えつかないような新規性の高い形状が生成され、既存の形にとらわれない製品設計につながります。
3Dプリンターをはじめとする生産・加工技術の進歩から、今後ますます注目されていく技術と言えます。
図8 トポロジー最適化を使用した形状設計例
代表的なソフトにはAltairの「OptiStruct」、Dassault Systèmesの「TOSCA」などがあります。
旭化成では「OptiStruct」を使用しています。
音響解析
音の発生、伝播に関係するさまざまな音響現象を解析し、可視化します。
スピーカーのような音響機器の音質向上だけでなく、エンジンやファンといった工業製品の騒音など不快な音への対策を設計に反映させることが可能です。音響特性に優れた製品や静粛性が求められる製品の開発には欠かせない解析です。
図9 音響解析例
代表的なソフトはHexagonの「Actran」、Dassault Systèmesの「Abaqus」などがあります。
旭化成では「Actran」を使用しています。
機構解析
有限要素法を使用した通常の解析では、部品単体での評価をします。しかし、複数の部品を組み合わせた製品では、部品を集合体として解析することが必要です。
機構解析では、他部品とのジョイント力の影響や、作用力を予測し、さらに動くことでどのような力が作用しているのかをシミュレーションすることができます。
自動車や産業機器など、複数の部品が複雑に結合している機械システムの評価に用いられています。
図10 機構解析例
出典:MSC社「接触解析」・「破壊及び損傷解析」ムービー内のモデル(2021年2月26日)
代表的なソフトはDassault Systèmesの「Simpack」、Hexagonの「Adams」です。
旭化成では「Adams」を使用しています。
繊維配向マッピング
樹脂にガラス繊維を配合した強化グレードでは、設計の際に繊維配向を考慮する必要があります。樹脂の流れに沿って繊維の向きが決まるため、収縮が不均一となって反りが発生したり、強度の弱い部分や方向が出てしまったりするためです。流動解析結果から、繊維方向・配向の情報をマッピングし、別の解析ソフトへ受け渡すことで応力解析の精度を高めることができます。
図11 繊維配向マッピング例
出典:Hexagon社ホームページ内 繊維配向マッピングモデル (2023年1月16日)
代表的なソフトはHexagonの「Digimat」です。
旭化成では「Digimat」を使用しています。
次回は「射出成形シミュレーション ~射出成形とは」についてご説明します。
CAEに関するお問いわせはこちらから