- TOP
- Basic knowledge engineering plastics
- What are polyamide resins (nylon resins)?
What are polyamide resins (nylon resins)?
An overview of the various types of polyamide resins and their characteristic physical properties
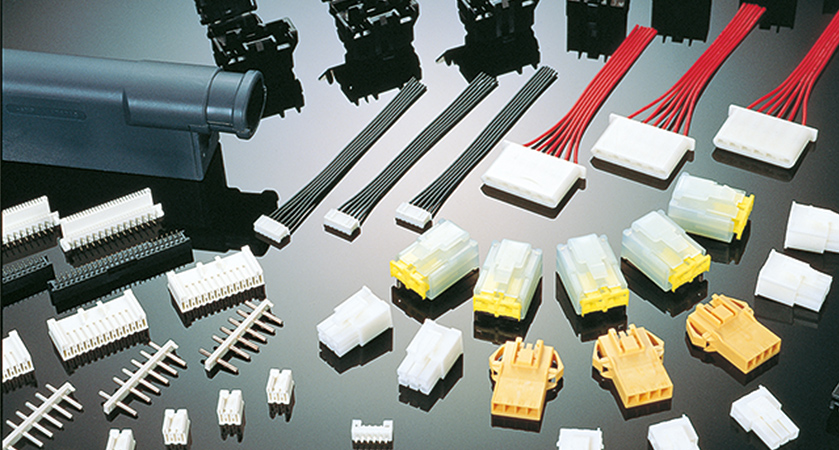
1. What are polyamide resins (nylon resins)?
Polyamide resins are thermoplastic polymer materials consisting of primary chains formed by repeated amide bonds (Figure 1). Polyamide materials are often known by the term nylon, a trade name introduced by Dupont—who carried out the world's first successful synthesis of polyamide 66—that has since become a common noun.
Polyamides were originally developed as materials for synthetic fibers, but their outstanding physical properties—including high mechanical strength, heat resistance, and chemical resistance—eventually led to their adoption as injection-molding materials for a broad range of applications, from automotive and industrial components to household appliances and beyond.
By selecting various types of monomers, including lactams, diamines, and dicarboxylic acids, polyamides can be made with a wide variety of molecular backbones. Here we will focus primarily on two crystalline polyamide resins that are widely used as general-purpose engineering plastics: polyamide 6 (PA6 or nylon 6) and polyamide 66 (PA66 or nylon 66).
Figure 1: Amide bonds.
2.Varieties of polyamides (nylons) and their nomenclature
As shown in Figure 2-1, there exist two types of process for producing polyamides: one in which the raw ingredients are carboxylic acids and amines, and another using dicarboxylic acids and diamines. Polyamides produced by the former approach are known as n-type polyamides, while the latter yields m,n-type polyamides.
For example, polyamide 6 is an n-type material synthesized via ring-opening polymerization of caprolactam, an intermediate compound produced by condensation cyclization of a carboxylic acid and an amine. The term "polyamide 6" derives from the fact that the number of carbon atoms between each amide bond [the total number of C atoms in the carbonyl and R (methylene) groups in Figure 2-1] is 6 (Figure 2-2).
On the other hand, polyamide 66 is an m,n-type material synthesized by condensation polymerization of adipic acid (containing m=6 carbon atoms) and hexamethylenediamine (containing n=6 carbon atoms), with amide bonds formed by dehydration reactions between carboxylic acids and amines (Figure 2-2).
Figure 2-1: The two types of polyamides and their synthesis.
Figure 2-2: Polymerization of polyamide 6 and polyamide 66
3.Key features of polyamide resins (nylon resins)
(1) Advantages
In general, polyamides offer the following outstanding physical properties.
・Excellent mechanical properties
・Excellent resistance to friction and abrasion
・Excellent heat resistance
・Excellent resistance to organic solvents
・High affinity for various substances, allowing blending with e.g., pigments, stabilizers, additives, and strength reinforcers.
・Excellent dielectric breakdown strength
On the other hand, polyamides can be difficult to use for the following reasons.
・Dimensions and physical properties of components may vary depending on humidity of usage environment.
・Prolonged exposure to moisture at high temperatures can degrade physical properties due to reduced molecular mass.
→ Click here for an overview and key properties of Asahi Kasei's LEONA™ polyamide resins
(2) The roles played by amide groups in the molecular chains comprising polyamides
a. Stronger bonds between molecules
As shown in Figure 3, hydrogen (H) atoms attached to nitrogen (N) atoms in amide groups exhibit affinity for oxygen (O) atoms in nearby molecular chains, leading to the formation of hydrogen bonds. Hydrogen bonds serve to constrain the relative positions of molecular chains, restricting molecular motion to increase strength and heat resistance (Figure 3). Reducing the number of carbon atoms (methylene groups)—denoted Rm and Rn in Figure 2 and indicated by dark circles in Figure 3—increases the proportion of amide groups and thus the prevalence of hydrogen bonds, thus tending to increase mechanical strength and heat resistance (yielding higher glass-transition points and higher melting points).
b. Increased toughness
The high affinity of amide groups for water tends to increase the water absorption of polyamides relative to other resins. When polyamides absorb water, their toughness increases due to the presence of water molecules between amide groups, but they also exhibit other, less desirable, changes, including dimensional variations, reduced glass-transition temperatures, and lower rigidity (Figure 3). Consequently, practical use of polyamide materials requires paying careful attention to the possibility of material-property variations caused by water absorption.
Figure 3: Configuration of water molecules and hydrogen bonds in polyamides
4.Applications of polyamide resins (nylon resins)
Polyamides are a particularly effective choice of materials for components surrounding automotive engines (Figure 4), where the superior heat resistance and oil resistance of polyamides allow components to remain stable in high-temperature environments while in contact with substances such as gasoline, lubricants, and anti-freeze agents. Polyamides are also ideal materials for components of gas intake/exhaust systems—which require high heat resistance—and for components requiring good electrical insulation, such as connectors in electrical systems.
Figure 4: Automotive engine chain case
Polyamides are also used for a wide variety of other types of products, including electric appliances, cooking tools demanding good heat resistance, temperature-control devices, and water-circulation systems. In addition, the use of polyamides for utility components such as zippers and cable ties can improve reliability and streamline assembly processes.
→ Click here to learn more about applications of Asahi Kasei's LEONA™ polyamide resins
5.Practical considerations regarding the use of polyamide resins (nylon resins)
Taking full advantage of the unique properties of polyamides requires paying careful attention to a number of practical considerations. Among the most important of these are proper moisture control during the formation process and awareness of the impact of moisture on product performance.
Figure 5 shows the results of an experiment quantifying dimensional variations in a formed polyamide component held at rest for a long period of time. In this experiment, a slab formed from polyamide was held for two years in a measurement chamber—with temperature and humidity uncontrolled—and measured at regular intervals. Starting from a fully moisture-depleted state, the dimensions of the slab increase over approximately the first six months due to water absorption and other factors. Thereafter, the slab dimensions vary periodically due to seasonal variations in temperature and humidity.
Figure 5: Long-term dimensional variation in polyamide 66 slab held at rest.
6.Varieties of polyamide resins (nylon resins) and how they are differentiated
As noted above, by varying the length of the lipid chain (methylene group) labeled R in Figure 3 it is possible to make polyamide materials with different performance properties. As explained in Section 3-2, reducing the number of methylene groups increases the proportion of amide groups and thus the prevalence of hydrogen bonds, with the ratio of methylene to amide groups influencing physical properties such as strength and heat resistance. More specifically, shorter R units yield increased strength and rigidity and higher melting points. Contrarily, longer R units allow molecular chains to move more easily and reduce water absorption due to the decreased prevalence of amide groups, which are responsible for water absorption in polyamides. In addition, different types of polyamides are made from different raw ingredients—some of which, as noted in the following section, may be biomass-derived. Figure 6 summarizes key data on various common polyamide varieties.
Figure 6:Types and characteristics of typical polyamide resins
7.Using biomass resources to make polyamide resins (nylon resins)
Polyamides are typically made from dicarboxylic acids and diamines, but plant-derived substances may also be biologically or chemically modified to yield raw ingredients for polyamides. The production of such biomass-derived polyamides is already underway at Asahi Kasei, with examples including polyamide 610—synthesized from hexamethylenediamine and sebacic acid—and polyamide 11, made from aminoundecanoic acid. Sebacic acid and aminoundecanoic acid are made from castor oil, a type of vegetable oil.
Asahi Kasei is also actively pursuing research efforts targeting industrial uses of metabolic pathways in microorganisms—with sugars as the primary ingredients—to yield biologically-derived precursors for polyamide production.
Column: Polar groups
Organic compounds contain covalent bonds (Figure 7), in which neighboring atoms share electrons to yield stable molecules. When the two atoms in a neighboring pair are identical—such as the C-C pairs at the left in Figure 8—the motion of their shared electrons is concentrated in the region precisely equidistant between the two nuclei. On the other hand, in neighboring pairs of different atoms, such as the C-X pairs at the right in Figure 8, the shared electrons feel different binding forces from the two nuclei and thus tend to localize closer to one of the two atoms. This is known as a polar group.
The different binding forces felt by electrons in polar groups give rise to electron-rich and electron-poor regions, which approach each other and attempt to become stabilized at an appropriate distance. In polyamides, the H region of NH pairs is electron-rich while the O region of C=O bonds is electron-poor, whereupon these regions settle into a stable state separated by a fixed distance; this enhances the force between molecules and helps to improve material performance.
Moreover, many inorganic compounds contain ionic bonds—and are thus quite compatible with plastics containing polar groups. This is the reason for the water-absorbing behavior of polyamides. Aside from water, the affinity of polyamides for glass fibers, colorants, flame retardants, and other additives allows the creation of specialized compounds offering a variety of functional properties.
Figure 7: Covalent bonding in molecular chain (shown here for polyethylene)
Figure 8: Polarization within polymer chains.
(Written by Isao Sato, Isao Sato Technical Office)
Asahi Kasei is dedicated to providing a full-fledged grade lineup of engineering-plastic products—and to exploiting our unique technological expertise to improve product performance. Please contact us to ask any questions, discuss any concerns, and request samples.
Please contact us to ask any questions, discuss any concerns, and request samples.