- TOP
- Basic knowledge engineering plastics
- What is polybutylene terephthalate (PBT)?
What is polybutylene terephthalate (PBT)?
An overview of polybutylene terephthalate (PBT): key properties and common applications
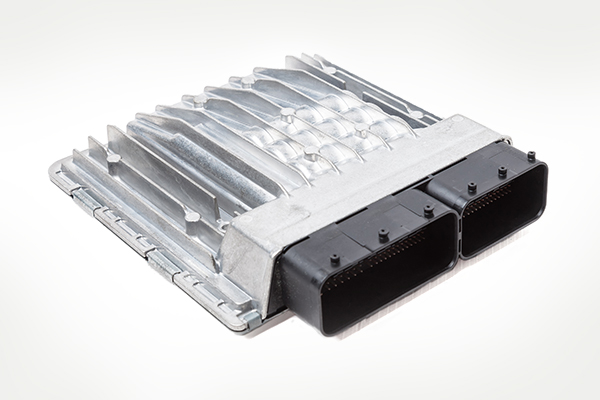
1.What is polybutylene terephthalate (PBT)?
Polybutylene terephthalate (PBT) is a crystalline material classified as a general-purpose engineering plastic. PBT, a type of polyester made from terephthalic acid and 1,4-butanediol, offers a number of excellent properties—including strong chemical resistance, desirable electrical properties, and high suitability for molding and other industrial processes—that have made it a common choice of material in a wide range of application domains, including electrical and electronic devices, automotive parts, and extrusion molding for films. On the other hand, the prevalence of ester bonds in PBT make it susceptible to degradation in the presence of strong alkalis and vulnerable to hydrolysis in warm, humid environments.
Esters are described by the chemical formula RCOOR' and may be formed by reacting an alcohol with an organic acid, as illustrated by the reaction scheme depicted below.
Figure 1: Reaction scheme for ester formation
Plastics consist of chain-shaped polymers; to produce long chains of esters, a divalent alcohol and a divalent organic acid are used as ingredients. This results in repeated formation of ester bonds via the reaction scheme shown below, resulting in a chain-shaped polymer.
Figure 2: Reaction scheme for formation of chain polymers
Research targeting practical applications of polyesters began with the study of fatty polyesters for synthetic fibers; however, materials formed in this way were unable to withstand the temperature of hot clothing irons—a key requirement for fibers—and thus could not be commercialized.
Sometime thereafter, the idea arose to improve heat resistance by adding aromatic rings, and this led to a material that could be used for fibers: polyethylene terephthalate (PET), made from terephthalic acid and ethylene glycol. Today, PET is widely used not only for synthetic fibers, but also for films, bottles, and many other products.
Although PET is sometimes used a material for molded products, the relative difficulty of crystallizing this material makes it inconvenient to form into complex shapes. To yield a material that could be efficiently molded into high-performance products, it was necessary somehow to stimulate the crystallization process—perhaps, for example, by blending crystallization-promoting additives into PET-based molding material.
Eventually, however, it was discovered that replacing the ethylene groups (C2) in PET with butylene (C4)—thus yielding polybutylene terephthalate (PBT)—gave a material that crystallized readily with no need for crystallization-promoting additives. This has made PBT a common choice of material for injection-molding applications in particular. Today PBT is made from terephthalic acid and 1,4-butanediol.
2.Key features of PBT
The ester bonds and aromatic rings in PBT ensure strong chemical resistance and good electrical properties, while PBT is also commonly blended with glass fibers or other fillers to improve mechanical properties and heat resistance.
- Excellent mechanical properties, particularly strength and toughness
- Can be reinforced with glass fibers or other fillers to improve rigidity, strength, and heat deflection temperature
- Low water absorption
- Excellent electrical properties
- Excellent chemical resistance (including resistance to organic solvents, weak acids, weak alkalis, and other agents)
- Low water absorption ensures minimal dimensional variation
Asahi Kasei also offers specialized PBT grades for various purposes, including grades reinforced with fillers, flame-retardant grades, impact-resistant grades, grades blended with various stabilizing additives, and high-cycle grades.
Practical considerations to keep in mind when considering PBT include the fact that long-term exposure to high temperatures in the presence of moisture can cause hydrolysis of PBT due to the ester bonds it contains. Also, PBT is not highly resistant to strong acid or strong alkali solutions. Consequently, the use of PBT in environments posing these dangers requires careful attention to all relevant risk factors.
3.Applications
The advantages outlined in the previous section have made PBT a widely-used choice of material for a variety of applications, including electrical and electronic devices, automotive components and automotive electrical systems, and extrusion molding for films.
Figure 3: Sample application of PBT materials: Connector for vehicle-mounted control unit
Figure 4: Sample application of PBT materials: Switch housing
4.Molding methods
The presence of residual water during the molding of PBT will induce hydrolysis. For this reason, the water content of the material to be molded must be reduced below 0.03%, and this in turn requires drying for sufficiently long times at high temperature (3 hours or more at 130°C). Vacuum dryers or desiccating dryers are commonly used.
PBT is a crystalline material with a melting point of 230°C, so for injection molding the cylinder temperature should be set to a resin temperature of 240-250°C.
Also, to ensure that molded bodies crystallize sufficiently and exhibit the high performance expected from PBT products, the mold temperature must be kept above 40°C. Due to the crystalline structure of PBT it is advisable to maintain sufficient pressure to avoid sink marks and warping.
5.Comparison of PBT and polyamide66
PBT and polyamide66 (PA66) are both crystalline engineering plastics widely used for applications demanding good heat resistance, high electrical insulation, strong chemical resistance, and other related properties. In practice, the correct choice for a given application depends on the different physical properties of these two materials, as summarized in Table 1.
Table 1: Comparison of key properties of PBT and PA66
Source: Prepared by Isao Sato from sources including page 520 of the Plastic Databook (Kogyo Chosakai Publishing Co., Ltd., in Japanese)
and pages 3-4 of Asahi Kasei's LEONA Handbook
Applications of PBT
As noted above, the high heat resistance and excellent electrical properties of PBT make it a widely-used material for electrical and electronic components.
Applications of PA66
Filler-reinforced PA66 exhibits higher mechanical strength and heat resistance than PBT, making this material a common choice for applications demanding unusually high heat resistance and strength, including electrical and electronic components as well as automotive structural components. Because PA66 materials have good sliding properties, they are often used to make moving parts required to exhibit high heat resistance.
Ultimately, the material properties of PBT and PA66 are rather similar, and each material manufacturer develops its own line of material grades in which the advantages listed above are enhanced—or in which the drawbacks noted above are mitigated. Thus the proper choice of material for a given application must often be determined on a case-by-case basis.
→Click here for an overview of Asahi Kasei's LEONA™ polyamide resins
6.Global warming and PBT
Techniques for obtaining the ingredients of PBT—terephthalic acid and 1,4-butanediol—from biomass material are a focus of ongoing research efforts. Also, the fact that polyesters can be polymerized via relatively simple procedures suggests the strong possibility of designing high-performance recycling systems capable of recapturing waste matter with only low levels of contaminants or foreign matter.
Column: The many varieties of polyesters
As discussed above, polyesters are produced by bonding a divalent alcohol with a divalent organic acid. The choice of which alcohol to combine with which organic acid may be made in various ways, yielding a variety of distinct polyester materials whose properties are summarized in Table 2.
PBT is synthesized from a fatty alcohol and an acid containing aromatic rings. This classifies PBT as a semi-aromatic polyester, with the aromatic rings contributing high heat resistance and good electrical properties. PET, widely used to make fibers, films, and bottles, also falls within this category.
Polyester is also used to make thermoplastic elastomers: block copolymers whose molecules contain both easily-deformable soft segments and deformation-resisting hard segments. In polyester-based thermoplastic elastomers (also known as thermoplastic copolyesters or TPCs), the hard segment is typically an aromatic polyester (often PBT), while the soft segment is typically a polyether (often PTMG), ensuring excellent heat resistance.
When both the acid and the alcohol used to make a polyester are fatty, the resulting polyester is biodegradable. Polylactic acid (PLA) is one example of a resin that has attracted intense interest as an environmentally-friendly material.
On the other hand, when both the acid and the alcohol used to make a polyester are aromatic, the resulting polyester may exhibit liquid-crystal behavior. Liquid-crystal polyesters (LCPs, also known as liquid-crystal polymers) have extraordinarily high heat resistance. As the melting point of a material approaches the temperature at which the material begins to decompose, the material becomes difficult to mold into specific shapes, but may be used as a heat-resistant high-performance material or as a fiber material.
Polyesters whose molecular chains incorporate double bonds are known as unsaturated polyesters. The double bonds in unsaturated polyesters can induce cross-linkages between molecular chains, yielding thermosetting plastics that are widely used as materials for large molded components in the construction and shipbuilding industries.
Table 2 Various polyesters
Created by Isao Sato based on the following documents, etc.
What is polyester? – Resin Plastic Materials Environmental Association (jushiplastic.com)
Saturated Polyester Resin Handbook, edited by Kazuo Yuki – Nikkan Kogyo Shimbun –
Polyester Resin Handbook, Eiichiro Takiyama/author – Nikkan Kogyo Shimbun –
Structure and biodegradability of aliphatic polyester, Masatsugu Mochizuki/Author – Textiles and Industry, Japan Textile Science Society –
(Written by Isao Sato, Isao Sato Technical Office)
Asahi Kasei is dedicated to providing a full-fledged grade lineup of engineering-plastic products—and to exploiting our unique technological expertise to improve product performance. Please contact us to ask any questions, discuss any concerns, and request samples.
Please contact us to ask any questions, discuss any concerns, and request samples.